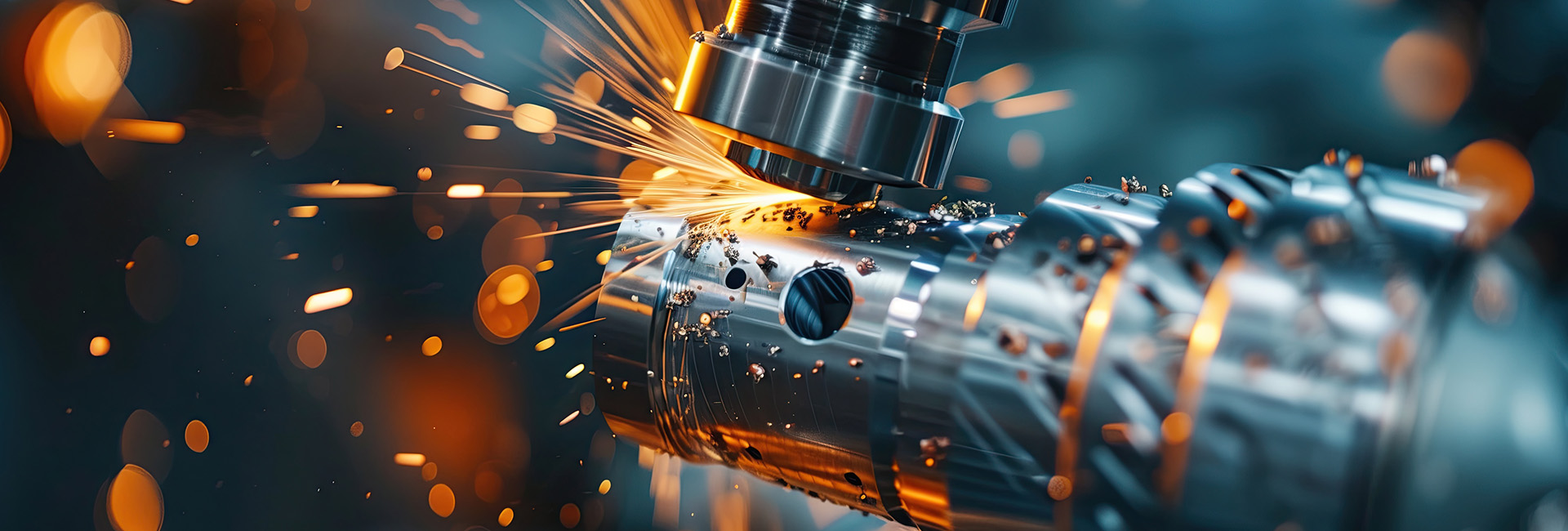
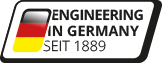
Tool Manufacturing
At Brüninghaus and Drissner, our tool manufacturing services specialize in the design, production, and maintenance of precision tools. The tool design phase begins with the creation of engineering drawings and 3D models, followed by simulations aimed at optimizing performance and durability. Prototypes are constructed and rigorously tested to validate and refine the design. Precision manufacturing is carried out using CNC machining centers, milling machines, lathes, and electrical discharge machines (EDM).
Selecting and testing suitable materials is essential to ensure tool quality. Regular maintenance is conducted to extend tool life, and repairs are performed as necessary. Optimization of existing tools involves analysis and implementation of improvements based on production feedback and advancements in technology. Surface treatments such as hardening processes and coatings are applied to enhance tool longevity.
Quality control and precise measurement technology ensure tool accuracy, while project management oversees the planning, coordination, and adherence to project timelines. Complete traceability is maintained through thorough documentation of all tools and their components. Training programs are offered to operating personnel, alongside technical consulting services to assist with the selection and implementation of new tooling solutions. These comprehensive services ensure the highest precision, efficiency, and quality in our tool manufacturing, ultimately improving overall production performance.
DIPL.-KFM. JÜRGEN DRISSNER
We offer you:
Design and Engineering
- Creation of engineering drawings and 3D models for tooling.
- Simulation and analysis of tool designs to optimize performance and durability.
Prototype Development
- Construction of prototypes to validate tool designs.
- Execution of test runs to refine the design
Tool Manufacturing
- High-precision manufacturing of stamping and forming tools.
- Utilization of CNC machining centers, milling machines, lathes, and EDM machines.
Material Selection and Testing
- Selection of appropriate tool materials based on specific requirements.
- Testing material properties to ensure tool quality.
Maintenance and Repair
- Regular inspection and maintenance to extend tool lifespan.
- Performance of repairs and adjustments when necessary.
Optimization and Improvement
- Analysis and enhancement of existing tools to improve efficiency and quality.
- Implementation of improvements based on production feedback and new technologies.
Surface Treatment
- Application of hardening processes and coatings to extend tool life.
- Use of surface treatments like nitriding, PVD, and CVD coatings.
Precision Measurement and Quality Control
- Use of high-precision measuring equipment to verify tool accuracy.
- Implementation of quality control measures during and after tool manufacturing.
Project Management
- Planning and coordination of complete tool manufacturing projects.
- Time and resource management to meet project milestones.
Documentation and Traceability
- Creation and maintenance of comprehensive documentation for each tool, including CAD files, inspection reports, and maintenance schedules.
- Ensuring complete traceability of all tools and their components.
Training and Consultation
- Training of operational personnel in the use of new tools and technologies.
- Technical consultation for the selection and implementation of tooling solutions.
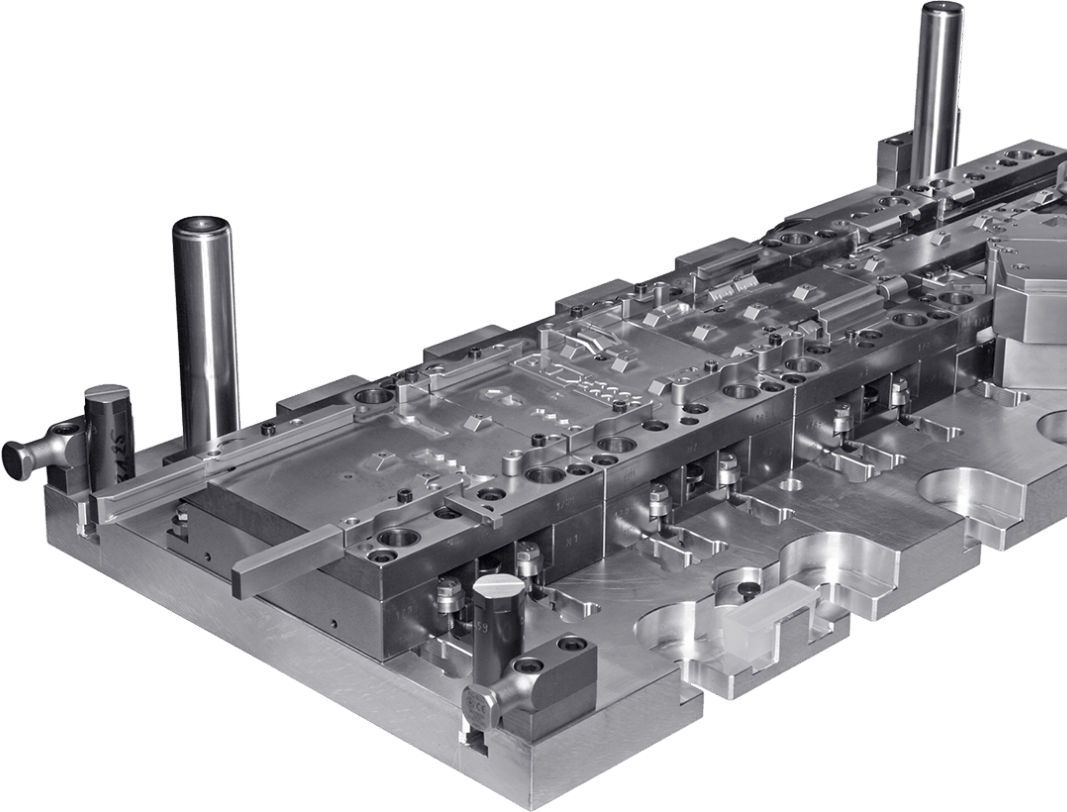