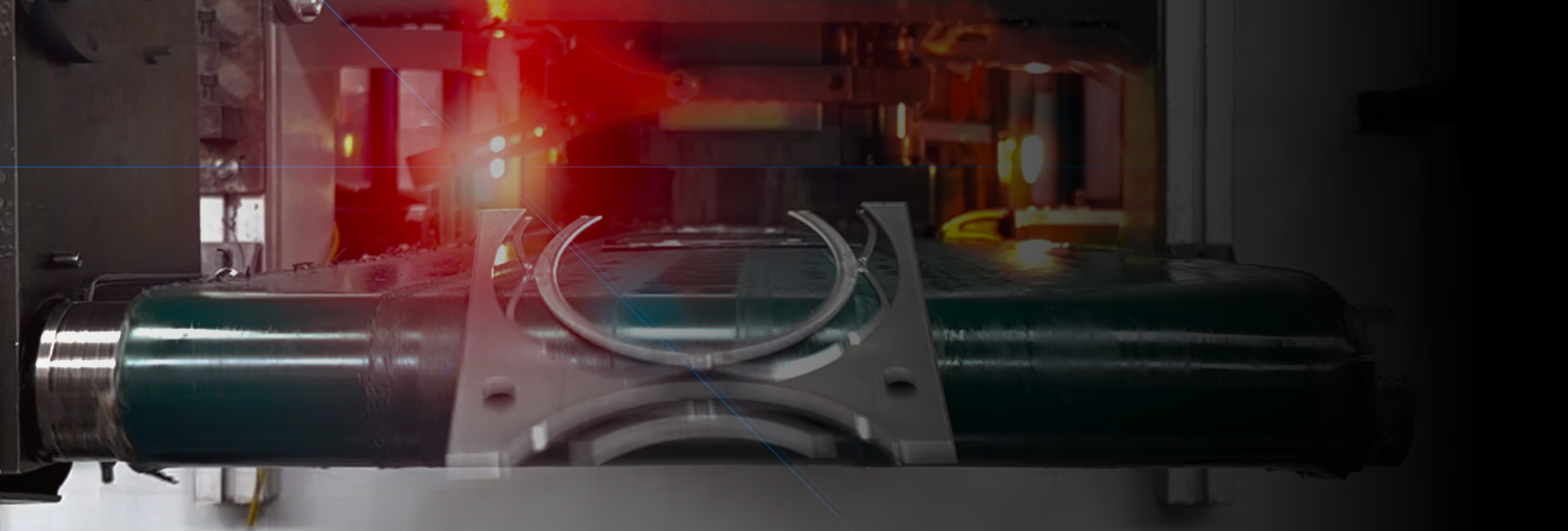
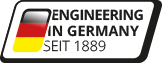
High-quality series production
Perfect results in any quantity!
Request Now
Serial Production
Series production requires the highest levels of precision, repeatability, and efficiency. As an experienced metal forming company, we offer customized solutions for small, medium, and large series – always with a focus on quality and cost-effectiveness.
Our customers benefit from optimized manufacturing processes that ensure maximum production reliability through modern machines, automated processes, and seamless quality control. This enables cost-effective manufacturing even with complex geometries and challenging materials.
With our state-of-the-art manufacturing technology and an experienced team, we guarantee reliable, economical, and high-quality production – for maximum customer satisfaction in every series!
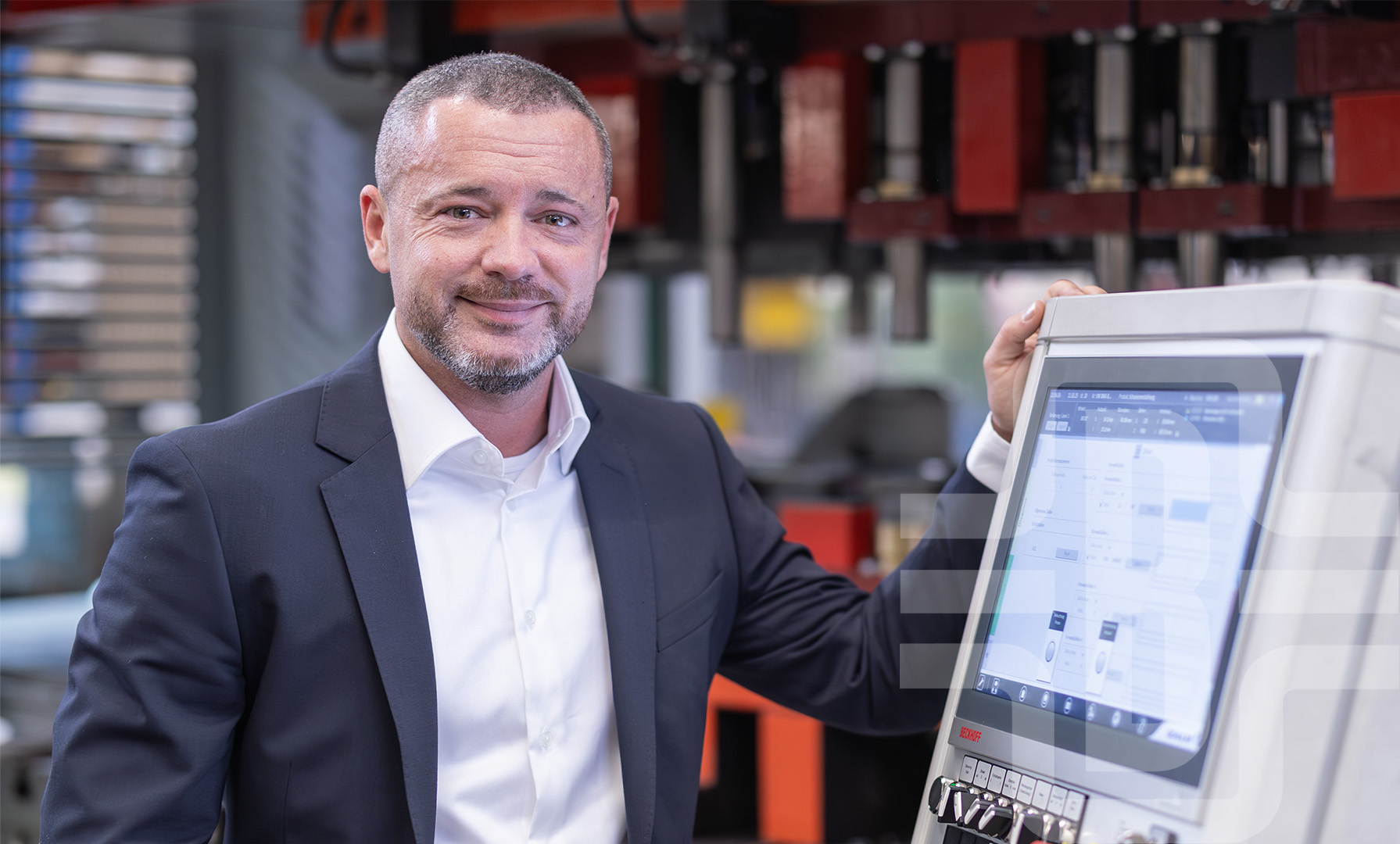
CERTIFIED TECHNICAL BUSINESS ADMINISTRATOR AMIR SAJNICA
Production Manager / Master Craftsman in Metal Construction / Welding SpecialistStamping and Forming Technology
Stamping and forming technology encompasses a wide range of services, from development support to production. This includes toolmaking and development support, including the design, manufacture, and maintenance of stamping and forming tools. The execution of stamping processes for the production of precision components and the application of various stamping techniques such as fine blanking and laser cutting are also central. Forming processes such as bending, deep drawing, embossing, and rolling, both cold and hot, play an important role.
The selection of suitable materials and their testing to ensure quality is also crucial. Production planning and control ensure on-time production and delivery, while quality control and assurance through inspections and tests ensure product quality. CNC machining using CNC machines enables precise machining, and the programming and operation of these machines are integral components. Assembly and finishing include the assembly of components and assemblies, as well as processes such as welding, soldering, coating, and surface treatment.
Process optimization through the analysis and improvement of existing production processes, as well as the implementation of Lean and Six Sigma methods, increase efficiency. Automation and robotics increase production capacity through the use of automation solutions and industrial robots. Logistics and warehousing organize material and parts logistics and optimize storage processes. Finally, customer-specific solutions are offered through the development support and manufacture of customized products, as well as the provision of consulting and technical support for special projects. These comprehensive services ensure efficient and high-quality production of precision parts and assemblies.
We offer you:
Stamping processes
- Performance of stamping processes for the production of precision components.
- Use of various stamping techniques such as fine blanking, progressive stamping, and laser cutting.
Forming processes
- Performance of forming processes such as bending, deep drawing, embossing, and rolling.
- Use of cold and hot forming processes.
Material selection and testing
- Selection of suitable materials for specific applications.
- Testing of material properties and ensuring quality.
Production planning and control
- Analysis and reduction of production costs through more efficient design and material utilization.
- Implementation of lean manufacturing principles.
Quality control and assurance
- Implementation of quality control procedures during production.
- Conducting inspections and tests to ensure product quality.
CNC machining
- Use of CNC machines for precision machining.
- Programming and operation of CNC machines.
Assembly and Processing
- Assembly of components and assemblies.
- Processing through welding, soldering, coating, and surface treatment.
Process Optimization
- Analysis and improvement of existing production processes.
- Implementation of Lean and Six Sigma methods to increase efficiency.
Automation and Robotics
- Use of automation solutions to increase production capacity.
- Integration of industrial robots into the manufacturing process.
Logistics and Warehousing
- Organization of material and parts logistics.
- Inventory management and optimization of warehouse processes.
Customized Solutions
- Development support and manufacturing of customized products according to customer requirements.
- Provision of consulting and technical support for customer-specific projects.
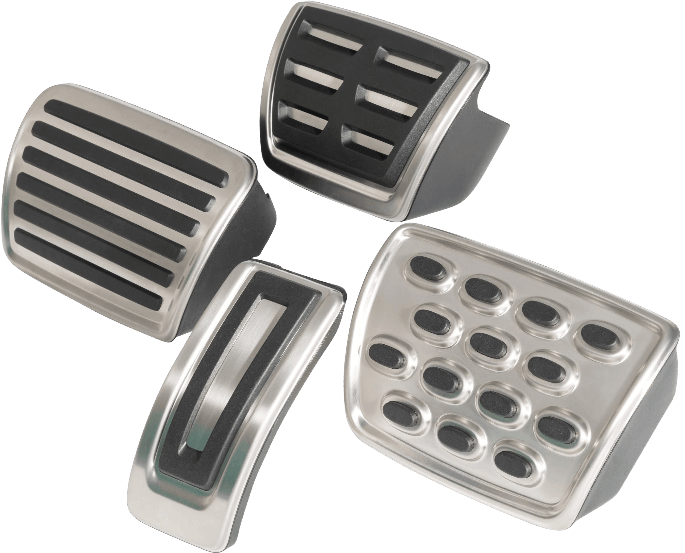
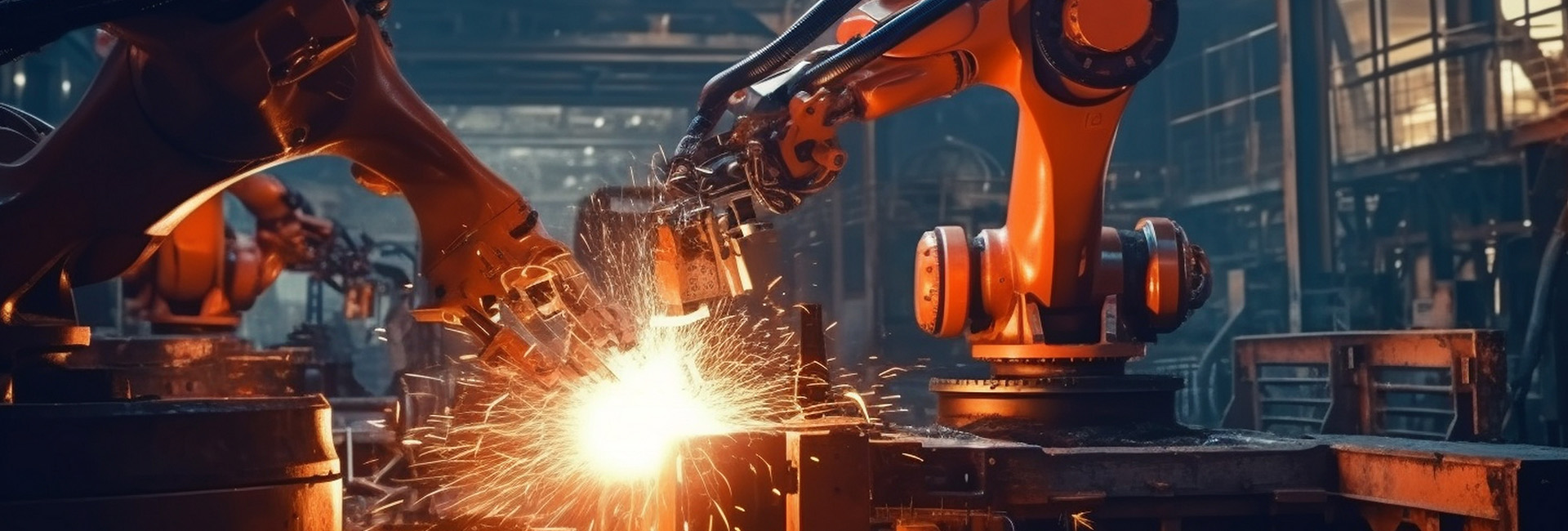
Welded Joints
To ensure precise and reliable welds, we offer a wide range of specialized services in this area. First, we select and apply various welding processes, such as MIG/MAG, TIG, spot welding, laser welding, and resistance welding, tailored to the specific material requirements and component geometries. Material preparation includes cleaning, degreasing, and adjusting the weld edges, as well as ensuring an optimal fit of the components.
Weld seam preparation includes beveling, splitting, and chamfering edges. Continuous monitoring and control is carried out during the welding process by qualified personnel and modern monitoring systems. Quality assurance involves visual inspections and non-destructive testing such as X-ray, ultrasonic, magnetic particle, and dye penetrant testing, accompanied by documentation and analysis of weld defects.
Post-treatment processes such as grinding, polishing, and annealing improve the properties of the weld, while corrosion protection measures increase durability. Weld seam testing and documentation, including mechanical tests such as tensile, flexural, and notched-bar impact tests, ensure strength and toughness. Welding procedures and personnel are qualified according to national and international standards, with welding procedure qualifications and welding procedure specifications being developed.
The use and programming of welding robots and the integration of automated welding systems into production lines increase efficiency. Finally, training and qualification of welding personnel in the latest techniques and processes includes continuing education opportunities for continuous improvement of employee skills and knowledge. These comprehensive services ensure that the welded joints are of the highest quality and meet the requirements of the automotive industry and other sectors.
We offer you:
Welding Processes
- Selection and application of various welding processes such as MIG/MAG, TIG, spot welding, laser welding, and resistance welding.
- Adaptation of welding processes to specific material requirements and component geometries.
Material Preparation
- Preparation of the components to be welded by cleaning, degreasing, and adjusting the weld edges.
- Ensuring optimal fit and securing of the components before welding.
Weld Seam Preparation
- Design and preparation of weld seams according to welding requirements.
- Carrying out weld seam preparation such as beveling, splitting, and chamfering of edges.
Welding Process Monitoring
- Continuous monitoring and control of welding processes by qualified personnel and modern monitoring systems.
- Use of measuring and testing equipment to verify welding parameters and quality.
Quality Assurance
- Performance of visual inspections and non-destructive testing (e.g., X-ray, ultrasonic, magnetic particle, and dye penetrant testing) to ensure weld quality.
- Documentation and analysis of welding defects and implementation of defect prevention measures.
Weld post-treatment
- Performing post-treatment operations such as grinding, polishing, and annealing to improve weld properties.
- Applying corrosion protection measures and surface coatings to increase durability.
Weld Inspection and Documentation
- Preparation of test reports and documentation for the traceability of welds.
- Conducting mechanical tests, such as tensile, flexural, and notched-bar impact tests, to verify the strength and toughness of welds.
Welding Procedure Qualification
- Qualification of welding procedures and personnel according to national and international norms and standards.
- Conducting welding procedure tests and preparing welding procedure specifications (WPS).
Welding Robots and Automation
- Use and programming of welding robots to automate welding processes and increase efficiency.
- Integration of automated welding systems into existing production lines.
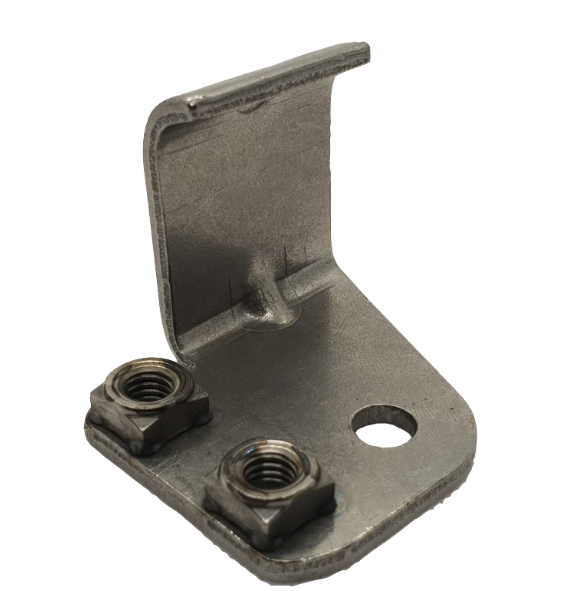
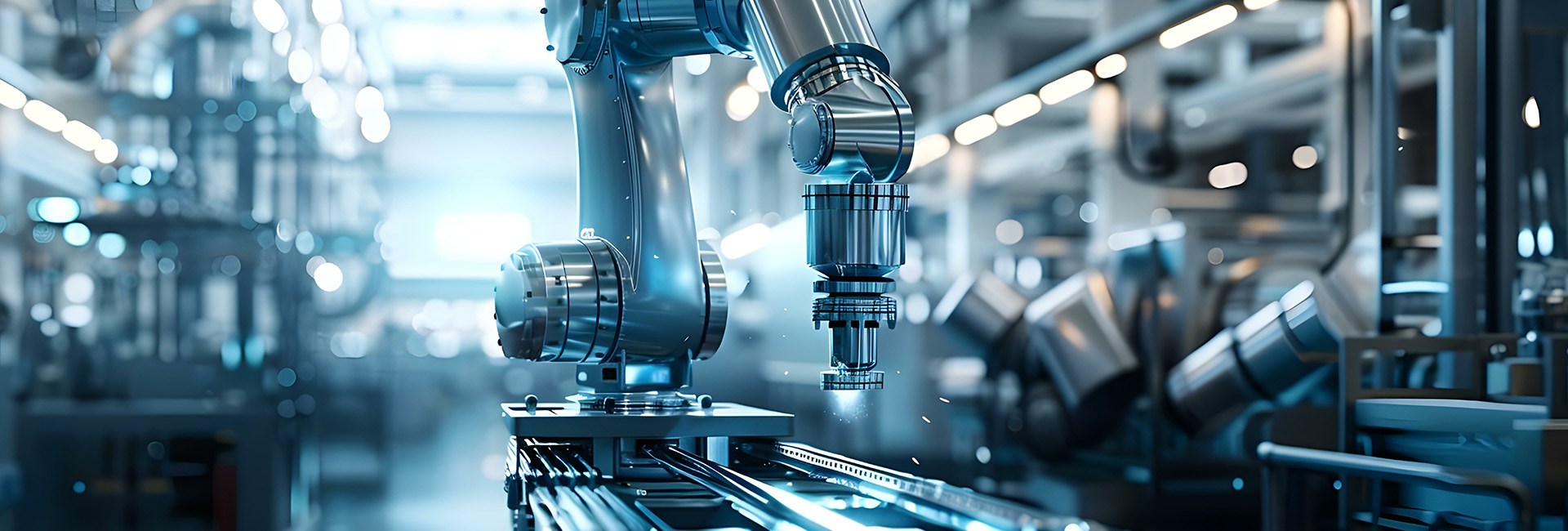
Assembly Manufacturing
At our company, assembly manufacturing encompasses a wide range of specialized services. First, assembly processes are planned and optimized, with assembly instructions and work instructions being created. Assembly itself involves the assembly of components and assemblies using techniques such as screwing, riveting, welding, and gluing. Automated assembly systems and robots are used and programmed to increase efficiency.
Quality controls are conducted during and after assembly to ensure compliance with all standards and specifications. Process optimizations, including the implementation of Lean and Six Sigma methodologies, aim to increase efficiency and reduce error rates. Specific tools and fixtures are designed, built, and maintained to support assembly processes.
Training and continuing education are critical to educate personnel on assembly processes and techniques and to improve their qualifications. Documentation of all assembly processes, changes, and improvements is carefully maintained. Ergonomic workplace design and safety measures are implemented to improve working conditions and productivity.
Logistics and material management also play an important role in ensuring the availability of all required parts for assembly and optimizing inventory and material flows. These comprehensive services ensure efficient, high-quality, and safe assembly of components and assemblies, while continuous personnel training and education ensures that employees always have the necessary skills and knowledge.
We offer you:
Assembly Planning
- Development support and optimization of assembly processes and procedures.
- Creation of assembly instructions and work instructions.
Assembly
- Assembly of components and assemblies into finished products.
- Application of various assembly techniques such as screwing, riveting, welding, and gluing.
Automated Assembly Systems
- Use and programming of automated assembly systems and robots.
- Integration of automated solutions into production lines.
Quality Control
- Conducting quality checks during and after assembly, including visual inspections and functional tests.
- Ensuring compliance with quality standards and specifications.
Process Optimization
- Analysis and improvement of existing assembly processes to increase efficiency and reduce error rates.
- Implementation of Lean and Six Sigma methodologies.
Tool and Fixture Manufacturing
- Development support and construction of specific tools and fixtures required for assembly processes.
- Maintenance and servicing of assembly tools and fixtures.
Training and Development support
- Training of personnel in assembly processes and techniques.
- Continuing education opportunities and training programs to improve employee qualifications.
Documentation
- Creation and maintenance of documentation for assembly processes, including work instructions, test protocols, and training materials.
- Documentation of changes and improvements in assembly processes.
Workplace Design
- Ergonomic design of assembly workstations to improve working conditions and productivity.
- Implementation of safety measures and compliance with occupational health and safety regulations.
Logistics and Material Management
- Planning and controlling material flows to ensure the availability of all parts required for assembly.
- Inventory management and optimization of material supply.
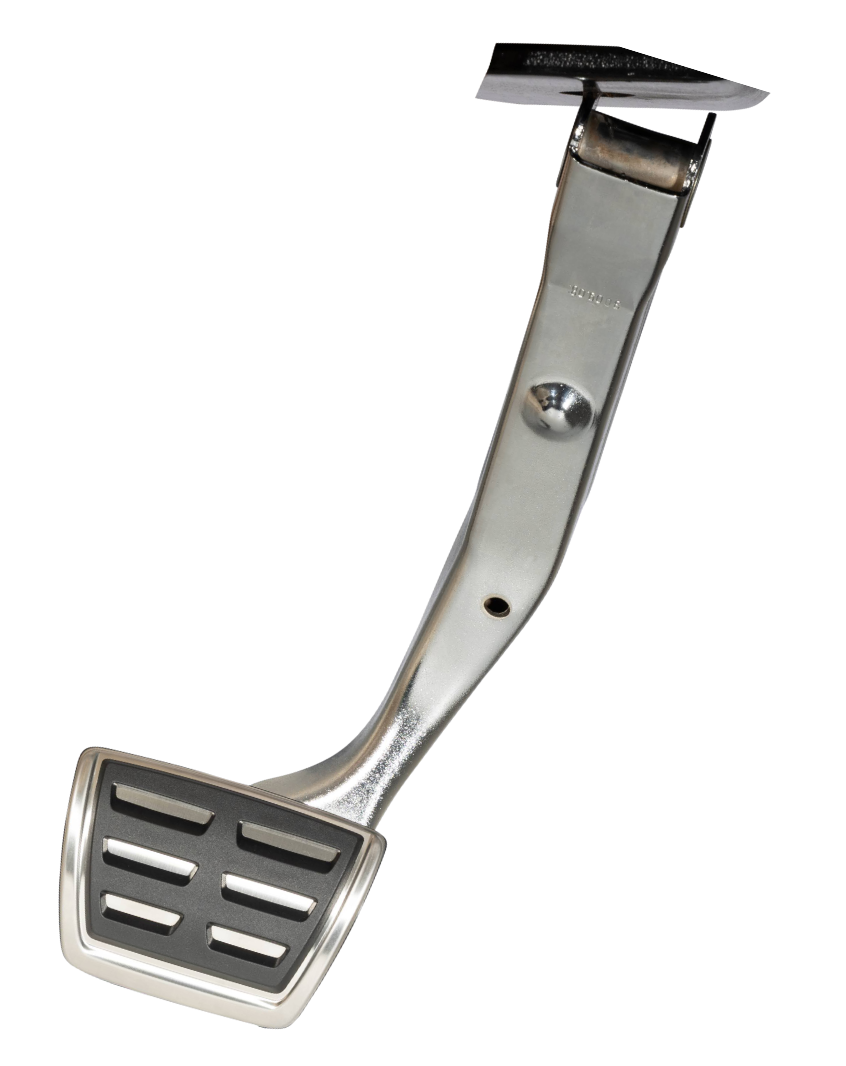
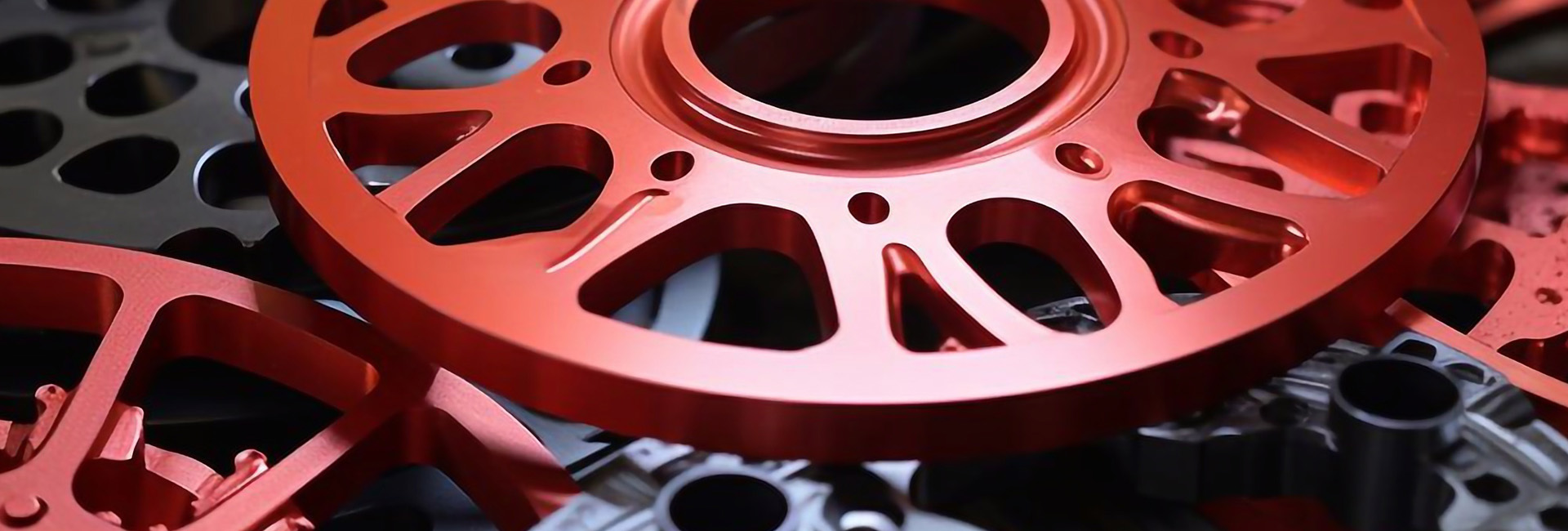
Surface Finishing
Surface finishing plays a crucial role in stamping and forming technology. It not only improves the appearance but also increases the durability, corrosion resistance, and service life of components. By using state-of-the-art processes, we ensure that every part meets our customers’ specific requirements – whether functional coatings or decorative finishes.
Our customers benefit from higher quality, longer durability, and improved performance of their products. Furthermore, our customized surface treatment enables optimal adaptation to individual requirements, whether for the automotive, electrical, or mechanical engineering industries.
With our comprehensive surface finishing, you receive components that not only impress with their functionality but also meet the highest aesthetic and quality standards.
We offer you:
Electroplating
(e.g., galvanizing, chrome plating, nickel plating) for optimal corrosion protection
Anodizing & passivation
to increase the durability of aluminum components
Powder coating & painting
for protection and visual enhancement
Hardening processes & plasma coatings
to increase wear resistance
Blasting, polishing & deburring
for a perfect surface
Individual consulting & customized solutions
for industry-specific requirements
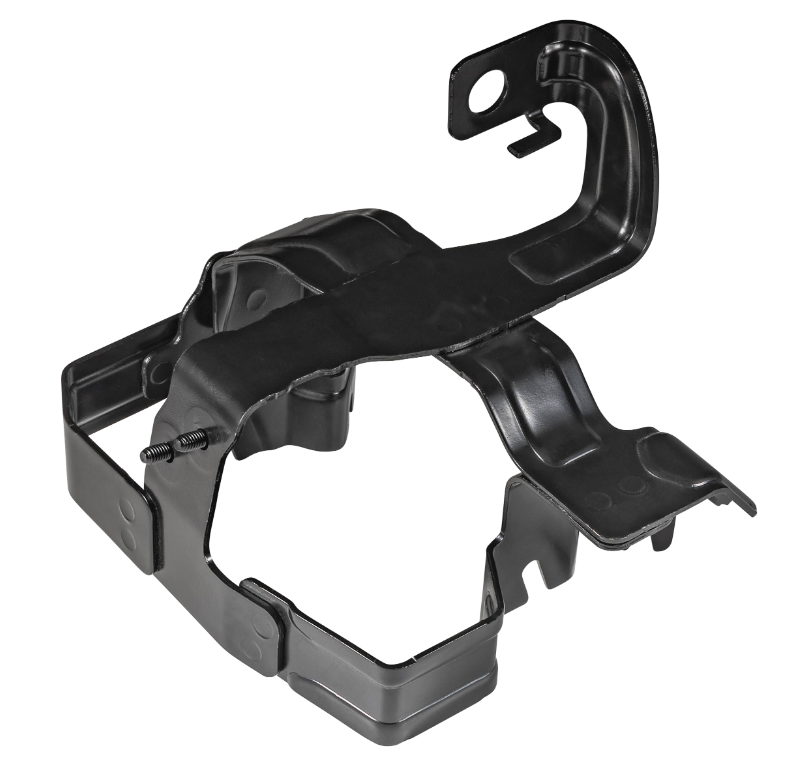