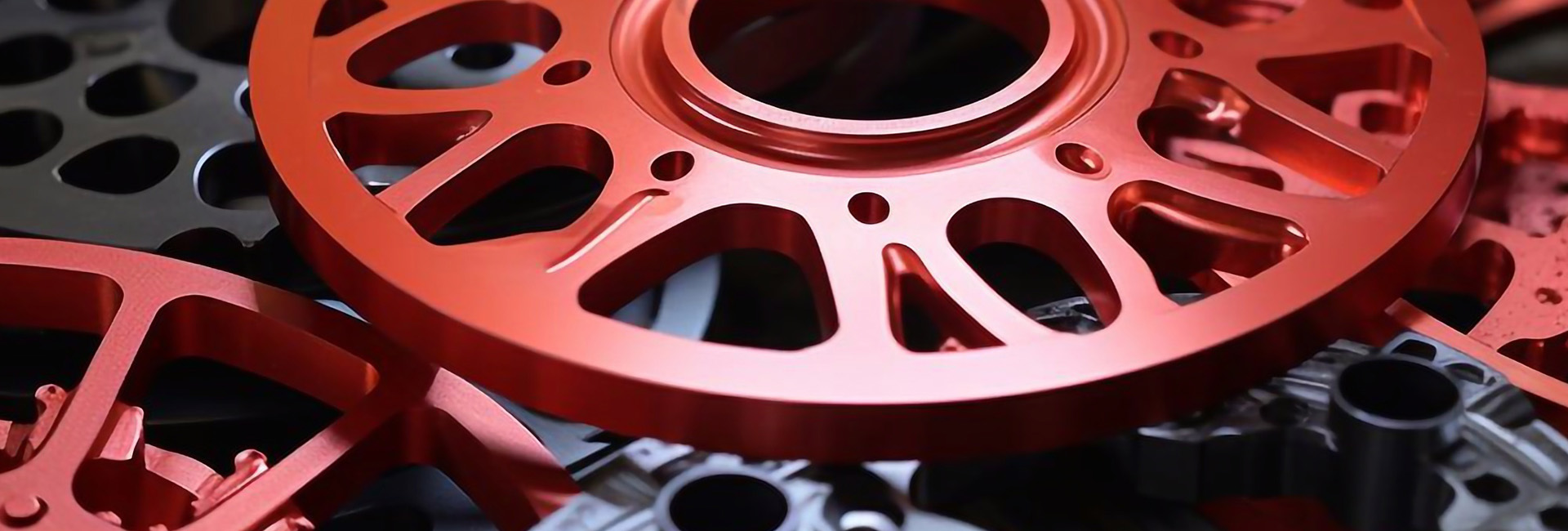
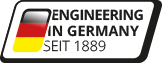
Coating
In stamping and forming technology, coating encompasses a range of specialized services aimed at enhancing component surfaces and optimizing their performance. The process starts with the selection and application of various coating types, including electroplating, chemical, thermal, or PVD/CVD coatings. Before the coating is applied, the surfaces are meticulously prepared through cleaning, degreasing, and possibly blasting to ensure proper adhesion.
The coating is then applied using methods such as spraying, dipping, or enameling, with close monitoring of coating thickness and uniformity throughout the process. Coating quality is verified through adhesion, corrosion, and wear tests to ensure all specifications are met. Additionally, suitable coating materials are selected and tested for properties such as hardness and corrosion resistance.
Regular maintenance and repair of coating equipment are essential to guarantee consistent quality. Documentation includes detailed records of processes, materials, and quality inspections. We also provide technical consultation and training to educate staff on best coating practices. Ongoing research and development focus on improving existing coating processes and discovering new solutions. These comprehensive measures ensure that coatings meet the required performance and protection standards.
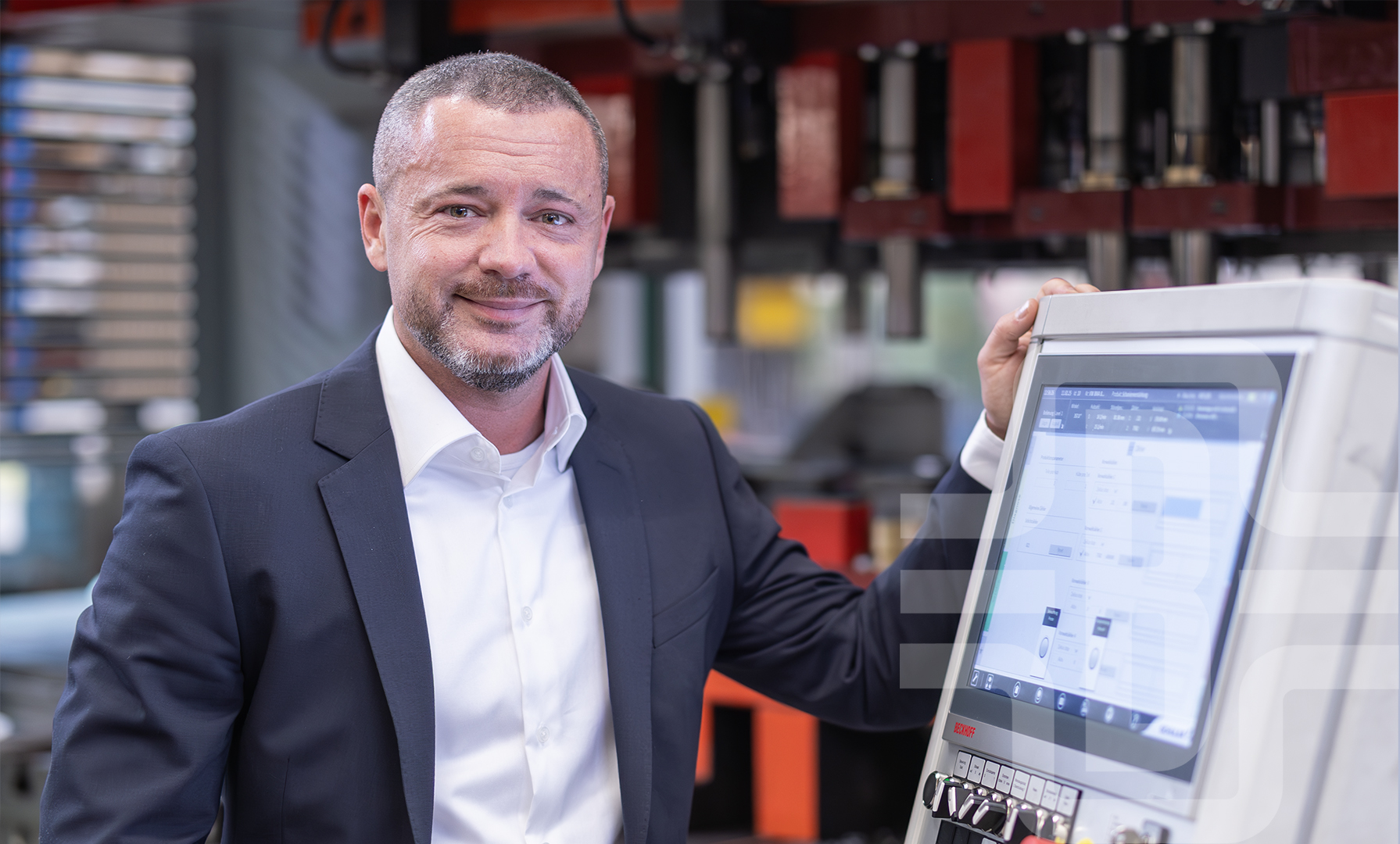
DIPL.-KFM. JÜRGEN DRISSNER
We offer you:
Coating Types
- Selection and application of various coating types, such as electroplating (e.g., galvanizing, nickel plating), chemical coatings (e.g., phosphating), thermal coatings (e.g., spray coatings), and PVD/CVD coatings.
Surface Preparation
- Preparation of surfaces through cleaning, degreasing, and blasting techniques to ensure proper adhesion.
- Execution of surface treatments such as sandblasting or pickling.
Coating Application
- Application of coatings using methods such as spraying, dipping, enameling, or specialized coating equipment.
- Control of coating thickness and uniformity during and after application.
Quality Control
- Implementation of tests to verify coating quality, including adhesion, corrosion, and wear tests.
- Ensuring compliance with required specifications and standards.
Material Selection and Testing
- Selection of appropriate coating materials based on application requirements.
- Testing of coating material properties, such as hardness and corrosion resistance.
Maintenance and Repair
- Maintenance of coating equipment to ensure consistent quality.
- Repair and recoating as needed.
Documentation
- Creation and maintenance of documentation for coating processes, materials, and results.
- Documentation of quality inspections and maintenance activities.
Consultation and Training
- Technical consultation on the selection of appropriate coating types and methods for specific applications.
- Training of personnel on coating processes and quality requirements.
Research and Development
- Development of new coating technologies and materials.
- Conducting research projects to improve existing coating processes and materials.
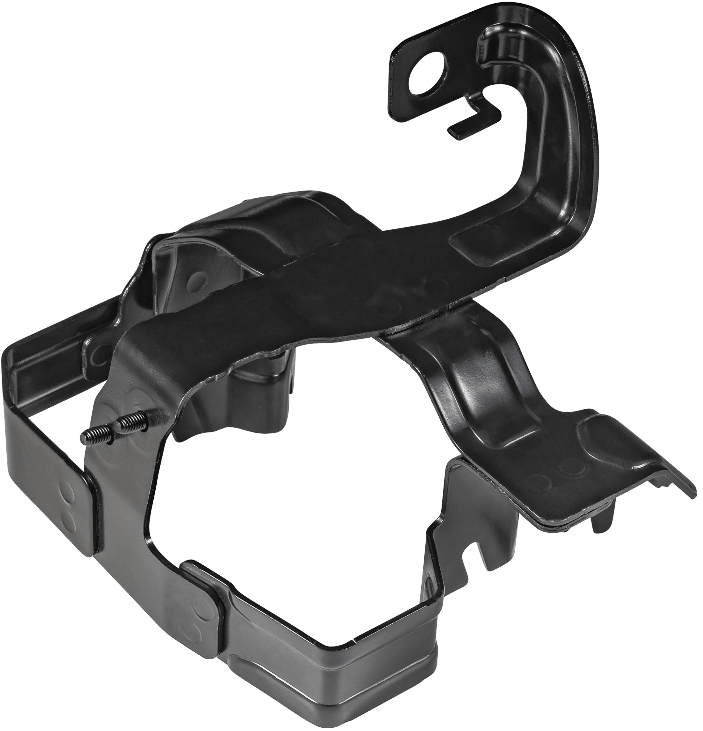